27 Feb 2023
Spandex
History of spandex fabric
In the United States, spandex is known by a different generic name and is often best known to consumers by brand names.
The history of spandex begins with the study of polyurethane in 1937 in Europe in the research laboratories of Otto Bayer. In 1939, Paul Schlack obtained a high-molecular polymer that made it possible to obtain fibres with high elongation and elastic properties. In 1951, W. Br. Enschede obtained the Vulkollan fibre through a process called 'wet spinning'.
In 1958 the 'dry spinning' process was developed at the DuPont laboratories in Wilmington. The first elastomeric fibre was patented in 1958 under the name 'K-fibre' and later branded as LYCRA; marketing began in 1962. Initially, Lycra fibre was used in medical stockings because the manufacturing technology of the time limited production to high count yarns. However, the potential of elastomers proved promising from the outset. In 1964, a renowned Italian fashion designer introduced a spandex fabric for swimwear, marking an important step forward in the use of this textile in the fashion world.
In the 1970s, research in this area focused on the possibility of producing finer fabrics, including spandex-based fabrics, but it was not until the early 1980s that elastomers entered the hosiery market, bringing a new level of comfort to stockings and tights.
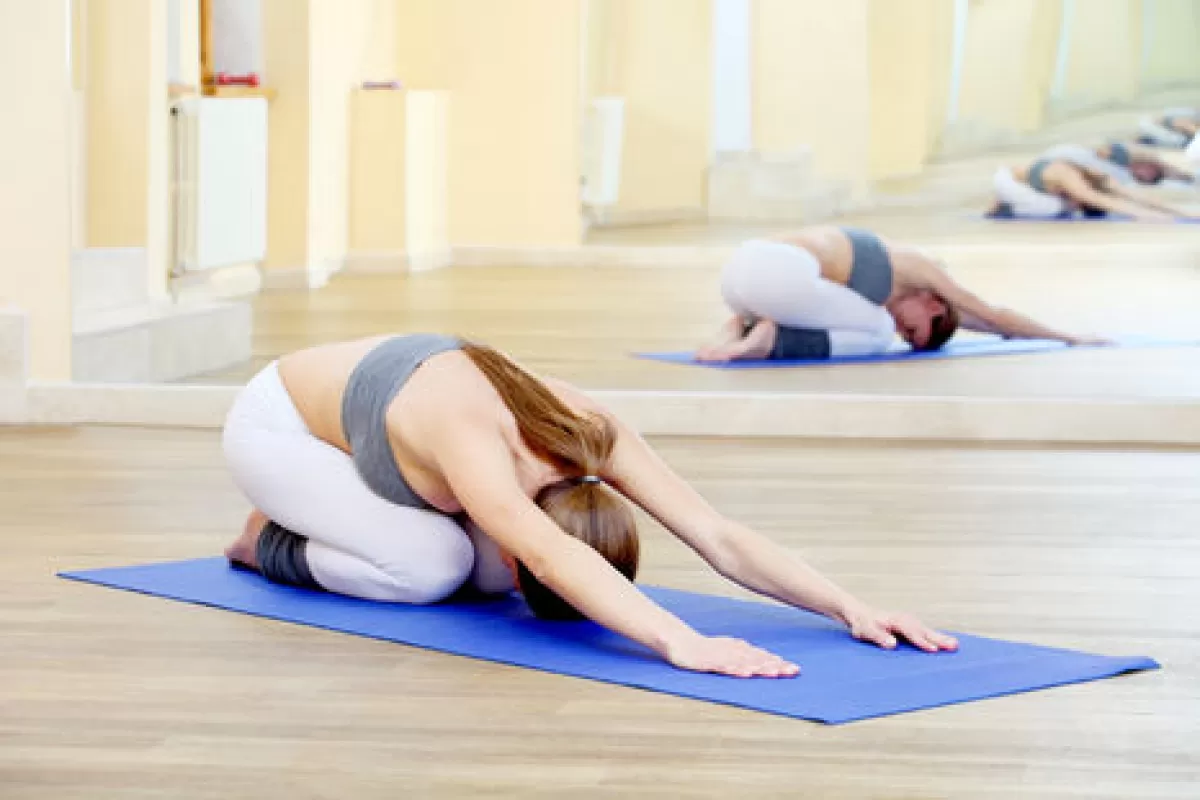
Curious about the composition of elastane
Did you know that Lycra, a type of elastane, is never used on its own? This elastic fibre is always combined with one or more other fibres, natural or synthetic. This allows stretch fabrics, including spandex fabrics, to retain the appearance and texture of the main fibre. LYCRA can be used in different proportions depending on the needs of the elastane fabric or its specific use. Interestingly, a minimum of 2% LYCRA is sufficient to significantly improve the quality of the final spandex product. This small percentage is enough to improve the vitality and drape of the fabric, as well as its ability to retain its original shape.

Spandex applications
Spandex textile can be used as a raw material without the need for further processing before being incorporated into hosiery and fabrics. A single strand of elastane is woven (textured) together with the knitted structure created by the main strand, whether plain or textured.
Another technique is to incorporate elastane, either in its raw or coated form, directly into the fabric through a process known as vanisé, where it also forms a type of knit. It is usually used in an alternating fashion, i.e. every other turn. Alternatively, the covered yarn can be used in every turn to provide elasticity in three dimensions.
In addition to its bare form, elastane is also covered. In this process, the spandex is wrapped around the main yarn, such as that used in nylon stockings or other materials, so that the spandex acts as the core of the yarn.
There are four types of coating:
- Single cover: the nylon or other fibre is spiralled around the spandex only once, with an average of 1,200-2,200 turns/metre; the higher the number of turns, the higher the quality.
- Double cover: the spandex thread is wrapped around two ends of nylon or other fibre, one clockwise, the other anticlockwise. The average number of twists per metre is 2,400, but can be as high as 3,000 in the highest quality yarns. It is used in yarns for the production of high quality sheer tights.
- Air-coating: the stretched spandex and textured nylon are passed through an air jet, interlacing the nylon with the spandex core at intervals.
- Core-spun: During the spinning process the spandex is covered with a set of discontinuous fibres.
YOU MAY ALSO BE INTERESTED...
The covered yarn is obtained by spirally winding Fulgar polyamide around LYCRA® fibre. The polyamide used can be parallel, textured multibava or microbava. The greater the number of windings, the higher the quality of the yarn obtained.
Characteristics of spandex used in fashion
Bare spandex yarn is used in standard fashion products. Used in the Vanisè process, bare spandex is suitable for the manufacture of very thin or summer tights, offering moderate elasticity which makes it possible to produce particularly light tights.
Coated spandex, on the other hand, is intended for the medium and high end of the market: the more protection applied to the spandex, the more durable and therefore more expensive the pantyhose, and the end product is also pleasantly soft to the touch.
You will not find tights made entirely of 100% spandex; other fibres such as nylon, cotton, wool or silk are always added in limited percentages.
The main characteristic of spandex is its high elasticity and ability to return to its original shape, ensuring excellent durability in fashion products. Spandex has the ability to stretch up to eight times its original length and return to its original shape immediately when the tension is released. This gives tights containing spandex a perfect fit on the legs while allowing complete freedom of movement. The greater elasticity of the fabric prevents both excessive stretching and loosening, which are the main causes of damage. It also does not require any special care during washing.
Nude elastane yarn is used in standard products. When used in the Vanisè process, nude spandex is suitable for the manufacture of very thin or summer tights, offering moderate elasticity which allows the tights to be easily removed.
To these basic qualities, manufacturers have added other properties such as resistance to chlorine, pollutants, chemicals and oxidants, as well as to mould and bacteria.

Origin:
Synthetic (EA).
Section:
Circular mono and multifilaments.
Title:
From 8 to 1,880 dtex.
Bright:
Brigtness, semi-transparent, transparent, dull. The greater or lesser sheen is determined by the use of bare or covered spandex. In pantyhose it also depends on the type of yarn that accompanies the spandex.
Elongation at break:
Above 200%; it is usually between 400 and 800%, depending on the type.